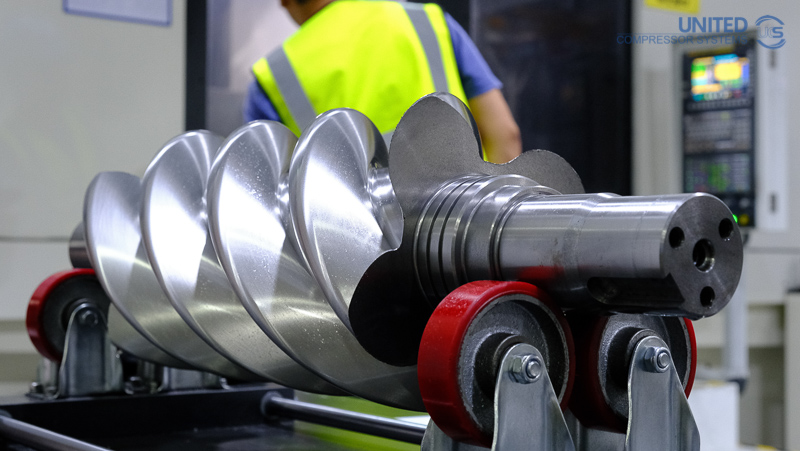
The UCT355-560 series two-stage compression air compressor equipped with T3851 air end developed by UCS has filled the technical gap of high-power screw air compressor with only water cooling but no air cooling. It has also obtained the third-party certification of Class-1 energy efficiency following "GB 19153-2019 Energy Efficiency Limit Value and Energy Efficiency Class of Volution-type Air Compressor".
Under the background of China's 2060 Carbon-Peak and Carbon-Neutral goal, the overall energy efficiency improvement of compressed air stations has become another decisive factor for many large enterprises and bidding projects. Considering the Class-1 energy efficiency, and with years of accumulated technology and experience in upgrading and renovating air compressor stations, UCS has landed several up-gradation projects for many enterprises in the past half-year, successfully converted the high energy-consumption air compressor stations for them. The up-gradation significantly improves the air supply stability for users and makes the overall energy efficiency of the air compressor station leap to Class-2 or even Class-1.
Case Introduction
A chemical enterprise in central China has two air compressor stations, 14 screw air compressors and 2 centrifuges, with total air consumption of about 1200m³/min and air pressure of 0.8mpa. According to the standard of "T/CGMA 033001-2018 Guidebook for Energy Efficiency Classification of Compressed Air Stations", the comprehensive energy delivery efficiency of the original air compressor stations was all less than the requirements of "Class-5 Energy-efficiency Air Compressor Station" due to various reasons. They were high energy-consumption air compressor stations.
After the UCS technical team made several on-site investigations and communicated with the users, the "compressed air Station overall up-gradation construction Scheme" was revised several times and finally approved by the users, standing out from many competitors to win the renovation project.
In July, a fleet of seven trucks carrying 14 UCS UCT500 series Class-1 two-stage air compressors started from the United & Hitachi plant to the user's site. After one month of installation, the acceptance test shows that the overall energy delivery efficiency of UCS 1200m³/min air compressor stations is as high as 55.6%, reaching the standard of the Class-1 energy efficiency and improving energy efficiency by 18% compared with the old stations.
After the renovation, the user calculated that the local average industrial electricity fee was ¥0.6/kWh. The annual continuous air consumption was about 8000 hours with average air consumption of 1200m³/min. After the renovation, the overall energy saving of the air compressor stations is 30,432,000 KWH, and the annual electricity saving is ¥18,259,200 (Equivalent to US$2,808,500).
Based on the calculation that 1 KWH = 0.997 kg carbon dioxide emission reduction = 0.272 kg carbon emission reduction, the annual carbon emission saving after the renovation is 8,277,504kg.
"We can save ¥18,259,200 in electricity costs and reduce more than 8,000 tons of carbon emissions a year. Our enterprise's savings in electricity costs can help further expand our production capacity and complete more sales orders. This renovation has a significant impact on our enterprise and will be promoted in the whole group in the later stage." said the user.